The manufacturing industry confronts unique financial and operational challenges, particularly when integrating acquisitions, standardizing financial reports and achieving precise financial forecasting. These tasks become even more intricate with the necessity for in-depth profitability analysis and the adaptation of project-based costing solutions for custom manufacturing processes.
The complexity and diversity of these processes demand specialized financial expertise and operational insights. Expert service providers and external consultants are crucial in tackling these challenges, offering a range of solutions from sophisticated financial modeling to the implementation of systems for accurate indirect cost allocation.
Their specialized knowledge of the manufacturing sector enables them to deliver bespoke strategies and solutions, ensuring financial operations are streamlined and strategically aligned with the company’s goals. This collaboration between manufacturers and financial experts is vital for enhancing financial clarity and operational efficiency.
Through the support of these specialized service providers, manufacturers can attain operational efficiency and financial clarity, fostering strategic growth and a competitive edge. This blog post explores the specific challenges within the manufacturing industry and showcases how solutions from external experts can convert these challenges into opportunities for optimization and expansion. With the right partnerships, manufacturers can effectively manage the complexities of financial planning and analysis, setting a strong foundation for future success.
READ MORE: Operational Due Diligence Resources for Manufacturing Businesses
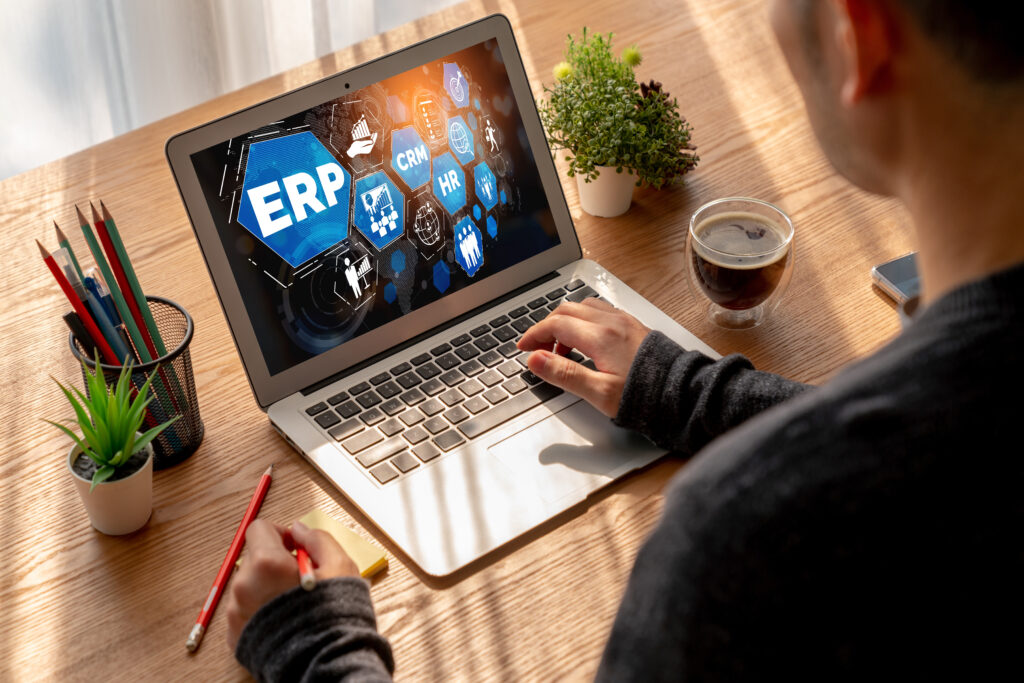
Streamlining Financial Forecasting, Reporting in Manufacturing
In the manufacturing sector, integrating acquisitions and standardizing financial reporting are monumental tasks. The complexity of merging diverse operational models leads to significant forecasting challenges.
Financial consultants with specialized expertise in manufacturing can offer advanced analytics and financial modeling to streamline these processes. They refine forecasting methods and enhance financial reporting clarity, ensuring that manufacturers can navigate post-acquisition transitions smoothly and align their financial strategies with operational realities.
Mastering Profitability Analysis
Understanding order and customer profitability is crucial for manufacturers, especially when indirect costs muddy the waters of financial clarity. The solution lies in implementing systems that accurately allocate indirect costs, enabling detailed profitability analysis at granular levels.
This is where cost accounting specialists come into play, developing and implementing methodologies that provide a clear picture of profitability, helping manufacturers make informed strategic decisions.
ALSO SEE: Finance Resources for Private Equity Firms, Leading Business Buliders
Enhancing Operational and Accounting Processes
Operational transitions, such as plant shutdowns, coupled with the need for accounting clean-up, present unique challenges.
Expert consultants in manufacturing operations and accounting can lead these efforts effectively. They conduct thorough root cause analyses and implement corrective actions, ensuring operational transitions are managed efficiently and accounting processes are optimized for accuracy and sustainability.
Redefining Cost Standards
For manufacturers, particularly in heavy industries like metals, outdated costing methods are a significant barrier to operational efficiency and profitability. Industry experts can assist in revamping cost standards, incorporating essential elements such as time studies, and establishing ongoing maintenance processes.
This comprehensive approach to cost standard revamping ensures manufacturers can accurately price their products and maintain competitive margins.
CASE STUDY: More Than $14 Million Saved in Procurement
Tailoring Project-Based Costing Solutions
Custom manufacturing processes require bespoke costing solutions, a challenge that standard ERP systems often cannot meet without customization. Specialized partners can assess the current state and fully implement product-based costing solutions tailored to the unique needs of custom manufacturers. This ensures that every project’s cost is accurately captured, enhancing financial visibility and strategic decision-making.
READ MORE: How To Extract Data from ERP Systems
The Business Builders’ Network is full of pre-vetted resources who are ready to help your company.
Our research and operations team already knows who you need before you contact us, and is prepared to connect you with a short list of industry-specific options.
Partnering with BluWave can not only gives you more confidence in your strategy, but we can help you get started within a single business day. Set up your scoping call today, and we’ll provide a short list of situation-specific resources who can help your business.